危废处理焚烧炉工艺流程图
危废处理焚烧炉工艺流程图简介:危废焚烧炉是焚烧处理危废的设备,垃圾在炉膛内燃烧,变为废气进入二次燃烧室,在燃烧器的强制燃烧下燃烧
危废处理焚烧炉工艺流程图简介:危废焚烧炉是焚烧处理危废的设备,垃圾在炉膛内燃烧,变为废气进入二次燃烧室,在燃烧器的强制燃烧下燃烧完全,再进入喷淋式除尘器,除尘后经烟囱排入大气。垃圾焚烧炉由垃圾前处理系统、焚烧系统、烟雾生化除尘系统及煤气发生炉(辅助点火焚烧)四大系统组成,集自动送料、分筛、烘干、焚烧、清灰、除尘、自动化控制于一体。
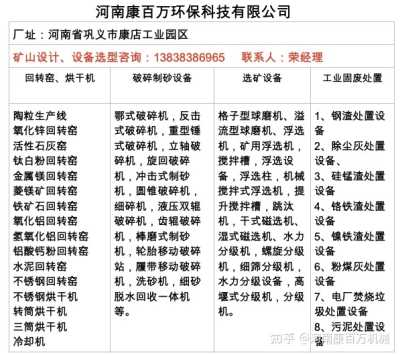
危废处理焚烧炉工艺流程图详解如下:
⑴工段名称:进料 工段简述:通过配伍、输送等步骤,使待处置废物合理搭配适合焚烧处置要求,有利于废物在后续焚烧过程中完全分解。
⑵工段名称:焚烧处置 工段简述:通过回转窑一次燃烧、二次燃烧等步骤,使危险废物能够在800—1300℃下完全焚毁,保证工艺控制中限定的99.999%的焚毁率。
⑶工段名称:烟气冷却 工段简述:通过余热回收、急速冷却等步骤,使二燃室排出的烟气温度降至200℃以下;余热回收主要是将烟气温度降至600℃,不得低于600℃,在降温过程中回收热源提供给厂区其他设施,保证热资源的再利用;急冷降温使烟气温度在一秒钟内由600℃降至200℃,最大限度减少二恶英的再合成。
⑷工段名称:尾气洗涤 工段简述:通过干、湿法两步脱酸确保酸性污染物去除效率;采用世界领先的膜分离技术与活性炭吸附技术有机结合,确保烟尘、二恶英、重金属等污染物去除效率。
⑸工段名称:尾气检测排放 工段简述:在线监测系统全程实时监控污染物排放情况,尾气排放达到GB18484-2001《危险废物焚烧污染控制标准》。
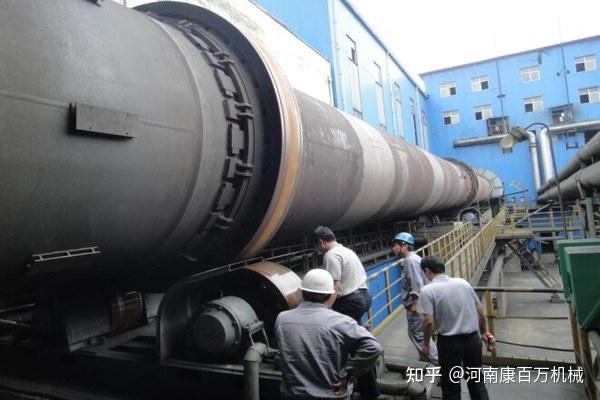
危废处理焚烧炉工艺流程图相关设备配置:预处理及进料系统---回转窑+二燃室燃烧系统---余热回收系统---尾气净化处理系统---烟气排放 焚烧系统:含料斗、回转窑,二次燃烧室,及助燃和风机等辅助 设备。 余热回收系统:含余热锅炉以及锅炉辅助系统设备。 烟气净化系统:冷却焚烧炉内的烟气并除去有害的物质,并且达到排放要求后排放。含急冷塔,除尘器,洗涤塔、烟气加热器、活性 炭供给系统、除灰渣系统等。 烟气排放系统:含引风机、烟囱等。
危废处理焚烧炉工艺流程图说明: 操作人员启动引风机预吹扫后,点燃燃烧器使炉内保持一定温度。当垃圾的热值较高时,燃烧器可以熄火;当垃圾的热值较低时燃烧器自动调节大小火,辅助燃烧。另外,助燃空气由鼓风机送入炉内,提供必需的氧气量。 在上述的燃料、水、空气供给正常后,待炉温升至一定高度,将医疗垃圾人工送入炉本体内。炉膛内的废弃物在燃料的助燃和小孔高压喷风作用下干燥、热解、燃烧。 焚烧炉本体中热解及燃烧后产生的烟气进入二次燃烧室,二次燃烧室实际上是一个气体燃烧炉,一次热解燃烧后的烟气中未燃烬的长链碳氢化合物及黑烟(有机碳)在二次风的挠动下,进一步湍流混合,在高温环境下可充分燃烧,使二恶英类有毒物质发生彻底分解。正常情况下二燃室中炉温大于850℃,设计总停留时间达2秒以上。烟气中的有机危害物被彻底破坏,转变为CO2、SOX、HCl等稳定的气体。 经充分燃烬后的烟气进入G-L热交换器中,利用夹套内冷却水吸收烟气热量降温,产生的热水可供生产或生活使用。烟气温度降至600℃左右,热交换器夹套水建议采用软化水,以免在管程上结垢影响换热效果、安全性及使用寿命。 经热交换降温后的烟气进入半干吸收塔,烟气中所含的酸性气体和喷淋雾化的碱液发生中和反应,烟气可以急速降温至200℃以下,避免二恶英的低温再生反应。 经初步净化的烟气进入活性炭反应器,在活性炭反应器内主要吸附烟气中的重金属二恶英及有害物质,夹带部分粉状活性炭及少量石灰粉尘进入布袋除尘器被收集下来,吸附在布袋上的碱性粉尘还能与烟气中的酸性物质进一步反应,脱除酸性物质。布袋除尘器的烟尘去除率可以达到99.9%,能达到国家规定的排放标准。收集下来的含有二恶英类的飞灰送至存灰间进行固化密封,定期送往垃圾填埋场填埋。净化的尾气由引风机抽引至烟囱排放。
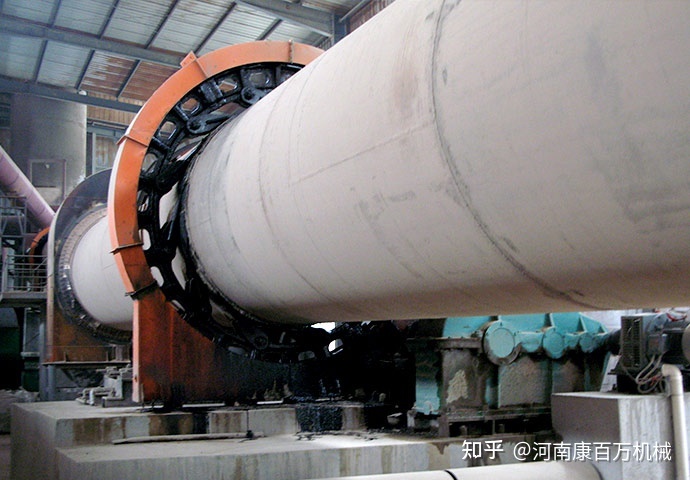
危废处理焚烧炉工艺流程图-固体危险废物预处理工艺的特点:
A、固体废物储存池进料门采用由红外线控制的自动控制密封门系统,在输送车进入储存区时密封门自动打开以便卸料, 卸料完成则密封门自动关闭, 确保储存池保持全密封的负压状态工作;
B、固体废物储存池采用钢砼混凝土结构,内覆多层防腐蚀材料,储存池的最低点设置渗沥水坑及泵;
C、在储存池内实现固体危险废物的储存、配伍及控制调节的过程
危废处理焚烧炉工艺流程图-液态危险废物的预处理工艺:
桶装废液与罐车废液通过真空系统和泵送系统输送至废液储罐中贮存。低热值废液焚烧前需通过配伍混匀, 调整热值和酸碱性。废液的配伍混匀在中和均质槽中进行。均质槽设置两个,带防爆搅拌器及夹套伴热,低热值废液储罐可通过管道自流至均质槽中。
危废处理焚烧炉工艺流程图-液体危险废物预处理工艺特点:
A、整个液体危险废物储存系统采用全自动的操作系统,有独立的操作室,与总控制室联网,实现总控制室人机界面的集中控制, 液体危险废物储存区域的卸料口及专用罐区均设置氮气保护装置,确保整个系统的安全;
B、系统设有均质槽以调节废液热值及酸碱度,可根据需要将液体危险废物送入焚烧系统;
C、桶装液体危险废物的储存设有专区,按照甲、乙类危险废物分开储存堆放,并就类别的不同区别存放, 输送采用真空输送系统, 只需将真空输送枪放入桶内, 桶内的液体危险废物将立即被吸入真空罐再由泵送往废液储罐。废液储罐采用热水夹套及保温, 并装有搅拌器。
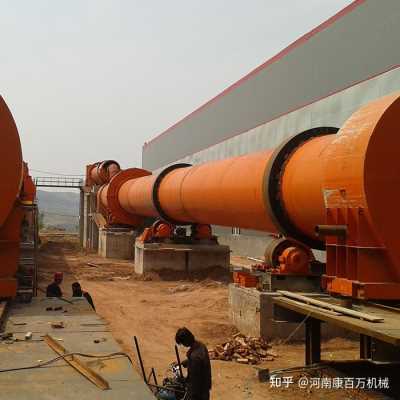
危废处理焚烧炉工艺流程图-膏状废物的预处理工艺:
桶装废液与罐车废液通过真空系统和泵送系统输送至废液储罐中贮存。低热值废液焚烧前需通过配伍混匀, 调整热值和酸碱性。废液的配伍混匀在中和均质槽中进行。均质槽设置两个,带防爆搅拌器及夹套伴热,低热值废液储罐可通过管道自流至均质槽中。
危废处理焚烧炉工艺流程图-液体危险废物预处理工艺特点:
A、整个液体危险废物储存系统采用全自动的操作系统,有独立的操作室,与总控制室联网,实现总控制室人机界面的集中控制, 液体危险废物储存区域的卸料口及专用罐区均设置氮气保护装置,确保整个系统的安全;
B、系统设有均质槽以调节废液热值及酸碱度,可根据需要将液体危险废物送入焚烧系统;
C、桶装液体危险废物的储存设有专区,按照甲、乙类危险废物分开储存堆放,并就类别的不同区别存放, 输送采用真空输送系统, 只需将真空输送枪放入桶内, 桶内的液体危险废物将立即被吸入真空罐再由泵送往废液储罐。废液储罐采用热水夹套及保温, 并装有搅拌器。
危废处理焚烧炉工艺流程图-危险废物进料系统进料系统流程及特点(固状、膏状、液状):
(1) 固体废物进料流程:
A、固体废物经起重机抓斗搅拌后,抓送至进料斗上方准备投料。
B、确定翻板处于全关状态,用抓斗将废物抓至翻板上部。
C、确定推料机处于全退状态、锁风装置处于全关状态,首先开启翻板,使固体废物落至推料机前端;关闭翻板, 然后开动推料机, 使固体废物进入回转窑前端, 而后推料机退后,根据实际情况确定往复操作的次数和频率,确保形成一定长度的窑前料封。
D、进入下一个固体废物进料流程,反复第(1)条至第(3)条的操作。
(2)膏状废物进料流程:
A、膏状废物、木糠混合固态物进料流程:
膏状废物、木糠经混合机出来的固态物的进料方式与固体废物进料方式相同, 参看固体废物进料流程。
B、包装膏状废物进料流程:
包装好的膏状废物通过滚柱传送装置运送到提升机上料搁板上, 由提升机提升至回转窑进料斗处,然后由推料机将纸袋(筒)推入回转窑,完成包装膏状废物的进料操作。
C、采用柱塞泵、喷枪进料流程:
回转窑前端设浆液喷枪, 利用柱塞泵的压力经喷枪喷入回转窑前端, 完成膏状废物的进料操作。
(3)、废液进料流程:
回转窑前端及二燃室设废液喷枪, 利用废液加压泵的压力实现废液雾化后经喷枪喷入回转窑前端或二燃室,完成废液的进料操作。
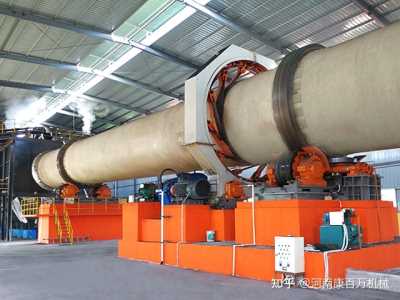
危废处理焚烧炉工艺流程图-焚烧系统:
焚烧系统流程及特点
A、危险废物均由回转窑前端进入回转窑,固体废物进料口、液态废物及混合料进料口喷枪均布置在回转窑窑头部位;
B、回转窑前端设有燃烧器和一次风,危险废物随着回转窑的转动不断翻滚,与一次风混合, 迅速被干燥并着火燃烧。同时在欠氧条件下分解出可燃气体, 焚烧产生的烟气进入二燃室;
C、回转窑中未燃烬的危险废物,从回转窑尾部落至设于二燃室下部的专用炉排上继续燃烧直至燃烬, 炉排的运行时间为可控, (根据排渣情况调整废物在炉排上的时间) 。产生的烟气进入二燃室,燃烬的炉渣落至水封式出渣机,炉渣经水冷却后,由炉渣运输车外运;
D、二燃室中设有两台喷油燃烧器、两个高热值喷枪和一组专门设计的二次风喷口,来自回转窑中未充分燃烧的气体进入二燃室继续燃烧, 二燃室布置了高速二次风, 它能有力地混搅烟气,并且在> 1100-1200 ℃的情况下,停留> 2 秒的行程时间,满足有害物质的充分燃烧和分界;
E、二燃室燃烧产生的烟气进入余热锅炉。本方案采用带尾部炉排的回转窑+二燃室组合式焚烧炉。该组合式焚烧炉具有下列适合危险废物焚烧的特点:
A、回转窑+二燃室结构是目前各国用于各种废物焚烧处置的最常用设备,有大量的使用业绩和较悠久的历史。
B、对危险废物的品种和热值均具有较好的适应性;
C、整个焚烧过程,在密闭的条件下进行,正常工作下为负压运行,无任何外泄情况发生,有效防止有害物质和恶臭对周围操作环境的污染;
D、在回转窑和二燃室内均布置燃烧器和助燃空气,确保危险废物在所要求的温度下进行燃烧;可以确保烟气在要求温度(≥ 1100℃) 以上具有不小于2 秒的停留时间, 使有毒有害气体彻底分解;
E、为了满足渣热灼减率< 5%的规定,在回转窑后续设一只专有技术的小炉排,未燃尽的物料可在炉排上继续焚烧一段时间。炉排是可调的,可以按实际情况加速或减速
危废处理焚烧炉工艺流程图-热能利用系统:
危废处理焚烧炉工艺流程图-热能利用系统流程:
A、二燃室出口高温烟气进入余热锅炉,在烟气降温的同时产生蒸汽,蒸汽从锅炉汽包排出,部分经过热器过热后进入高温分汽缸进行蒸汽的分配使用, 另一部分即从汽包引出饱和汽进入低温分汽缸以供使用。
B、经余热锅炉降温后的烟气(约500~600℃)进入烟气净化系统。
危废处理焚烧炉工艺流程图-余热锅炉特点:
为了大幅度降低运行成本, 工程采用一台特殊的全辐射式余热锅炉, 该锅炉是在总结了国内、外以焚烧危险废物余热锅炉的应用实践中, 不断改进而开发的全辐射式余热锅炉, 它具有以下特点:
A、根据工程的特点,为了有效降低运行成本,锅炉的供汽采用两种参数,即:设计压力为1.6MPa,饱和蒸汽温度为203℃;系统中设计了两种分汽缸,即:低温分汽缸及高温分汽缸(详见: 工艺流程图) ;高温分汽缸出来的蒸汽设计压力是1.5MPa,过热蒸汽温度为:360℃,并利用该过热蒸汽对炉排风及二燃室二次风均加温至: 200~300℃,提高了系统的燃烧热效率;并利用该过热蒸汽把烟气处理系统SCR 系统的进口烟气温度加热到:240℃-250℃,克服了如用饱和蒸汽加热须加电热带进行再升温,大幅度降低了运行成本。
B、该锅炉特别适应烟气温度向更高化的变化,即使烟气温度超过1100℃或更高,锅炉出口温度的变化也不会太大。
C、锅炉不会出现因积灰和堵灰而导致的影响运行状况,所以锅炉能长期稳定运行,确保降低烟气温度和连续供应工艺生产系统和生活用蒸汽。
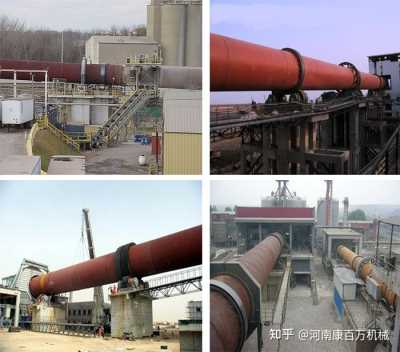
危废处理焚烧炉工艺流程图-烟气净化系统:
危废处理焚烧炉工艺流程图-固废处置烟气净化工艺,包括:
A、烟气冷却:将烟气通入急冷塔进行冷却,利用喷液在高温气流中的蒸发达到使气流降温的目的,将炉气温度由500-600℃降到200℃以下,所用的喷液是来自于喷淋吸收塔排出的废碱液,其中所含碱液能对气体中酸性成份起中和脱酸作用,效率可达到60-80%。
B、干式脱酸:为了除去烟气中汞等金属及其蒸汽和二恶英的有害物质,在急冷中和塔和布袋除尘器之间的烟道上设置有活性炭粉喷射系统。活性炭粉经容积给料机, 输送至特别设计的喷射吸收器。同时,还配置了活性消石灰( Ca(OH)2)的喷射系统,与活性碳混合后喷入吸收器, 通过特制的文丘里烟气管道, 能达到50%除SO2效率和70%以上除HCL、HF效率。碱性物与烟气反应产物的回收利用,继续用于对烟气处理。
C、除尘:将经过b 步骤处理的烟气通入袋式除尘器,确保了灰尘颗粒在10mg/m3 以下的除尘要求。
D、脱硝:将经过c 步骤处理的烟气先经过加热器加热后通入设有喷氨装置的脱硝器,采用SCR(选择性催化剂脱硝工艺) 。依靠催化剂的作用,加强氨( NH3)对NOx 的吸收,达到脱NOx 的目的,效率可以达到85%。
E、湿式脱酸:将经过d 步骤处理的烟气通入设有碱液喷淋装置的湿式吸收塔,使SO2,HCl、HF 的去除率都可以达到99%。同时,还可以去除气流中残存的粉尘。e 步骤中的碱液在与烟气反应后回收至急冷塔作为急冷塔冷却剂;
F、烟气加热:将经过e 步骤处理的低温烟气加热至130℃,防止低温饱和烟气在引风机中以及烟囱凝结造成对设备、烟道及烟囱的腐蚀以及“白烟”现象出现。
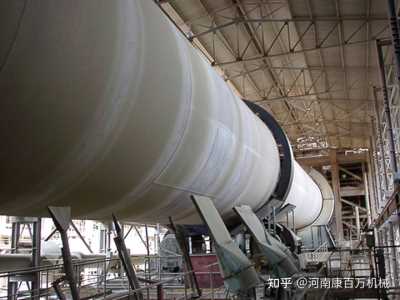
危废处理焚烧炉工艺流程图-烟气处理工艺具有以下优点:
A、急冷塔中所需的冷却剂碱液不必制备,只需利用湿式脱酸处理后的废液就可进行烟气冷却以及初步的脱酸;
B、活性炭和消石灰进行混合后作为干法脱酸的吸附剂, 可以省去活性炭吸附这套工艺;
C、干法脱酸工艺所产生的副产物易于处理,也可投入消石灰与活性炭的混合器中,作为吸收剂循环使用,节约吸收剂用量;
D、干法脱酸工艺是在特制的文丘里管道中完成, 利用其特性能很好的对烟气进行处理;
E、湿式吸收塔中所产生的废液,可以投入急冷中和塔中代替冷却水作为冷却剂使用,不必专门设置废液处理系统,节省工艺,节约资源消耗;
F、整套烟气处理工艺采用急冷——干法——布袋除尘—— SCR——湿法, 能够很好的处理成分复杂、颗粒细小、技术要求高的烟气;
G、通过加热烟气,可防止低温饱和烟气在引风机中以及烟囱凝结造成对设备、烟道及烟囱的腐蚀和“白烟”现象的出现。
危废处理焚烧炉工艺流程图危险废物焚烧处置系统应包括预处理及进料系统、焚烧炉、热能利用系统、烟气净化系统、残渣处理系统、自动控制和在线监测系统及其它辅助装置。
1.2危险废物在焚烧处置前应对其进行前处理或特殊处理,达到进炉要求,以利于危险废物在炉内充分燃烧。
1.3 对于处理氟、氯等元素含量较高的危险废物,应考虑耐火材料及设备的防腐问题。对于用来处理含氟较高或含氯大于5%的危险废物焚烧系统,不得采用余热锅炉降温,其尾气净化必须选择湿法净化方式。
1.4 整个焚烧系统运行过程中要处于负压状态,避免有害气体逸出。
1.5 危险废物焚烧厂设计服务期限不应低于20年。
危废处理焚烧炉工艺流程图- 预处理及进料系统
2.1 危险废物入炉前需根据其成分、热值等参数进行搭配,以保障焚烧炉稳定运行,降低焚烧残渣的热灼减率。
2.2 危险废物的搭配应注意相互间的相容性,避免不相容的危险废物混合后产生不良后果。
2.3危险废物入炉前应酌情进行破碎和搅拌处理,使废物混合均匀以利于焚烧炉稳定、安全、高效运行。对于含水率高的废物(如污泥、废液)可适当进行脱水处理,以降低能耗。
2.4 在设计危险废物混合或加工系统时,应考虑焚烧废物的性质、破碎方式、液体废物的混合及供料的抽吸和管道系统的布置。
2.5 危险废物输送、进料装置应符合下列要求:
(1) 采用自动进料装置,进料口应配制保持气密性的装置,以保证炉内焚烧工况的稳定;
(2) 进料时应防止废物堵塞,保持进料畅通;
(3) 进料系统应处于负压状态,防止有害气体逸出;
(4) 输送液体废物时应充分考虑废液的腐蚀性及废液中的固体颗粒物堵塞喷嘴问题。
危废处理焚烧炉工艺流程图-焚烧炉
3.1 危险废物焚烧可根据危险废物种类和特征选用不同炉型。
3.2 危废处理焚烧炉工艺流程图-危险废物焚烧炉的选择应符合下列要求:
(1) 焚烧炉的设计应保证其使用寿命不低于10年;
(2) 焚烧炉所采用耐火材料的技术性能应满足焚烧炉燃烧气氛的要求,质量应满足相应的技术标准,能够承受焚烧炉工作状态的交变热应力;
(3) 应有适当的冗余处理能力,废物进料量应可调节;
(4) 焚烧炉应设置防爆门或其它防爆设施;燃烧室后应设置紧急排放烟囱,并设置联动装置使其只能在事故或紧急状态时才可启动;
(5) 必须配备自动控制和监测系统,在线显示运行工况和尾气排放参数,并能够自动反馈,对有关主要工艺参数进行自动调节;
(6) 确保焚烧炉出口烟气中氧气含量达到6%-10%(干烟气);
(7) 应设置二次燃烧室,并保证烟气在二次燃烧室1100℃以上停留时间大于2s;
(8) 炉渣热灼减率应<5%;
(9) 正常运行条件下,焚烧炉内应处于负压燃烧状态;
(10) 焚烧控制条件应满足国家《危险废物焚烧污染控制标准》(GB18484-2001)中的有关规定。
3.3 燃烧空气设施的能力应能满足炉内燃烧物完全燃烧的配风要求;可采用空气加热装置;风机台数应根据焚烧炉设置要求确定;风机的最大风量应为最大计算风量的110%—120%;风量调节宜采用连续方式。
3.4 启动点火及辅助燃烧设施的能力应能满足点火启动和停炉要求,并能在危险废物热值较低时助燃。
.3.5 辅助燃料燃烧器应有良好燃烧效率,其辅助燃料应根据当地燃料来源确定。
3.6 采用油燃料时,储油罐总有效容积应根据全厂使用情况和运输情况综合确定;供油泵的设置应考虑一备一用;供油、回油管道应单独设置,并应在供、回油管道上设有计量装置和残油放尽装置;采用重油燃料时,应设置过滤装置和蒸汽吹扫装置。
危废处理焚烧炉工艺流程图-热能利用系统
4.1 焚烧厂宜考虑对其产生的热能以适当形式加以利用。
4.2 危险废物焚烧热能利用方式应根据焚烧厂的规模、危险废物种类和特性、用热条件及经济性综合比较后确定。
4.3 利用危险废物焚烧热能的锅炉,应充分考虑烟气对锅炉的高温和低温腐蚀问题。
4.4 危险废物焚烧的热能利用应避开200~600℃温度区间。
4.5 利用危险废物焚烧热能生产饱和蒸汽或热水时,热力系统中的设备与技术条件应符合国家《锅炉房设计规范》(GB50041-1992)中有关规定。
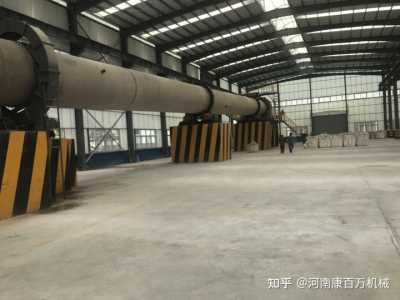
危废处理焚烧炉工艺流程图-烟气净化系统
5.1 烟气净化技术的选择应充分考虑危险废物特性、组分和焚烧污染物产生量的变化及其物理、化学性质的影响,并应注意组合技术间的相互关联作用。
5.2 烟气净化系统可根据不同的废物类型及其组分含量选择采用半干法烟气净化和湿法烟气净化方式。
(1) 半干法净化工艺:包括半干式洗气塔、活性炭喷射、布袋除尘器等处理单元,应符合下列要求:
① 反应器内的烟气停留时间应满足烟气与中和剂充分反应的要求;
② 反应器出口的烟气温度应在130℃以上,保证在后续管路和设备中的烟气不结露。
(2) 湿法净化工艺:包括骤冷洗涤器和吸收塔(填料塔、筛板塔)等单元,应符合下列要求:
① 必须配备废水处理设施去除重金属和有机物等有害物质;
② 为了防止风机带水,应采取降低烟气水含量的措施后再经烟囱排放。
5.3 烟气净化装置应有可靠的防腐蚀、防磨损和防止飞灰阻塞的措施。
5.4 酸性污染物包括氯化氢、氟化氢和硫氧化物等,应采用适宜的碱性物质作为中和剂,在反应器内进行中和反应。
5.5 除尘设备的选择应根据下列因素确定:
(1) 烟气特性:温度、流量和飞灰粒度分布;
(2) 除尘器的适用范围和分级效率;
(3) 除尘器同其它净化设备的协同作用或反向作用的影响;
(4) 维持除尘器内的温度高于烟气露点温度30℃以上。
5.6 烟气净化系统的除尘设备应优先选用袋式除尘器。不得使用静电除尘和机械除尘装置。若选择湿式除尘装置,必须配备完整的废水处理设施。
5.7 袋式除尘器应注意滤袋和袋笼材质的选择。
5.8 危险废物焚烧过程应采取如下二恶英控制措施:
(1) 危险废物应完全焚烧,并严格控制燃烧室烟气的温度、停留时间和流动工况;
(2) 焚烧废物产生的高温烟气应采取急冷处理,使烟气温度在1.0秒钟内降到200℃以下,减少烟气在200~600℃温区的滞留时间;
(3) 在中和反应器和袋式除尘器之间可喷入活性炭或多孔性吸附剂,也可在布袋除尘器后设置活性炭或多孔性吸附剂吸收塔(床)。
5.9 活性炭或多孔性吸附剂及相关设备应具有兼顾去除重金属的功能。
5.10 对于含氮量较高的危险废物必须考虑氮氧化物的去除措施。应优先考虑通过焚烧过程控制,抑制氮氧化物的产生;焚烧烟气中氮氧化物的净化方法,宜采用选择性非催化还原法。
5.11 引风机应采用变频调速装置。
5.12 经净化后的烟气排放和烟囱高度设置应符合《危险废物焚烧污染控制标准》(GB18484-2001)要求。
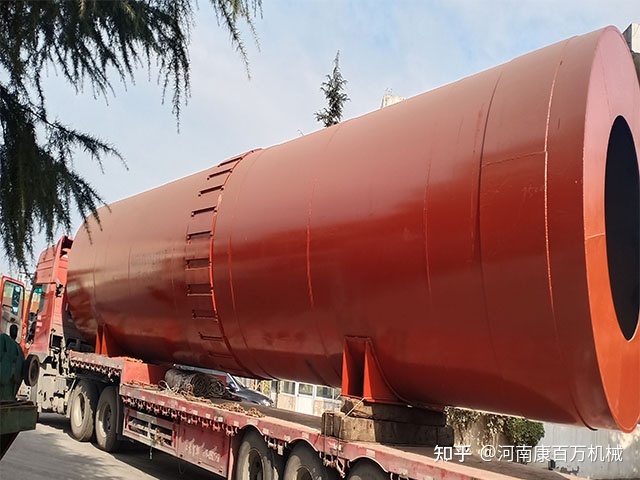
危废处理焚烧炉工艺流程图- 残渣处理系统
6.1 焚烧残渣(包括炉渣和飞灰)应按危险废物进行安全处置。对于根据国家《危险废物鉴别标准》(GB5085.1~3-1996)鉴别后不属于危险废物的炉渣可按一般工业废物处置。飞灰必须经过稳定化处理后再进行安全填埋。
6.2 残渣处理系统应包括炉渣处理系统、飞灰处理系统。炉渣处理系统应包括除渣冷却、输送、贮存、碎渣等设施。飞灰处理系统应包括飞灰收集、输送、贮存等设施。
6.3 炉渣与飞灰的生成量应根据废物物理成分、炉渣热灼减率及焚烧量核定。
6.4 残渣处理技术选择与规模确定,应根据炉渣与飞灰的产生量、特性及当地自然条件、运输条件等,经过技术经济比较后确定。
6.5 残渣处理系统应有稳定可靠的机械性能和易维护的特点。
6.6 炉渣处理装置的选择应符合下列要求:
(1) 与焚烧炉衔接的除渣机应有可靠的机械性能和保证炉内密封的措施;
(2) 炉渣输送设备应有足够宽度。
6.7 炉渣和飞灰处理系统各装置应保持密闭状态。
6.8 烟气净化系统采用半干法方式时,飞灰处理系统应采取机械除灰或气力除灰方式,气力除灰系统应采取防止空气进入与防止灰分结块的措施。采用湿法烟气净化方式时,应采取有效的脱水措施。
6.9 飞灰收集应采用避免飞灰散落的密封容器。收集飞灰用的贮灰罐容量宜按飞灰额定产生量确定。贮灰罐应设有料位指示、除尘和防止灰分板结的设施,并宜在排灰口附近设置增湿设施。
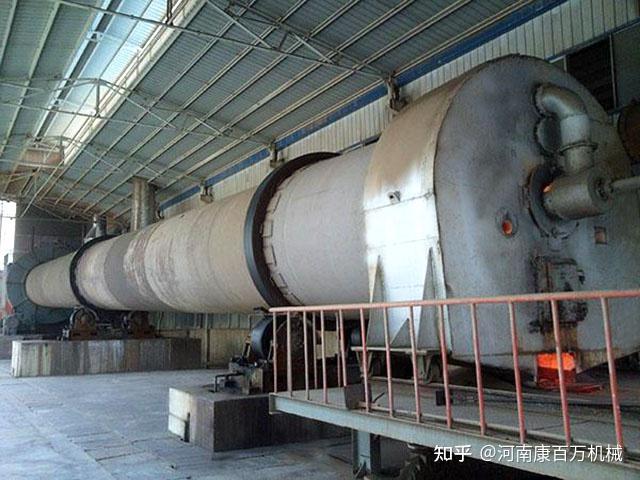
危废处理焚烧炉工艺流程图-自动化控制及在线监测系统
7.1 焚烧厂的自动化控制系统必须适用、可靠,应根据危险废物焚烧设施的特点进行设计,并应满足设施安全、经济运行和防止对环境二次污染的要求。
7.2 焚烧厂的自动化系统应采用成熟的控制技术和可靠性高、性能价格比适宜的设备和元件。设计中采用的新产品、新技术应在相关领域有成功运行的经验。
7.3危险废物集中焚烧处置应有较高的自动化水平,能在中央控制室通过分散控制系统实现对危险废物焚烧线、热能利用及辅助系统的集中监视和分散控制。
7.4 自动控制的主要内容应根据焚烧厂的规模和各工艺系统的设置情况确定。一般可包括:进料系统控制、焚烧系统控制、热能利用系统控制和烟气净化系统控制等。
7.5 对不影响整体控制系统的辅助装置,可设就地控制柜,必要时可设就地控制室,但重要信息应送至中央控制室。
7.6 对贮存库房、物料传输过程以及焚烧线的重要环节,应设置现场工业电视监视系统。
7.7 对重要参数的报警和显示,可设光字牌报警器和数字显示仪。
7.8 应设置独立于分散控制系统的紧急停车系统。
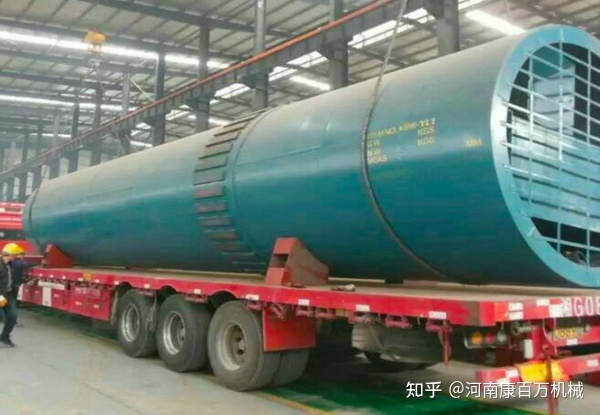
危废处理焚烧炉工艺流程图回转窑焚烧炉主体部分为卧式的钢制圆筒,圆筒与水平线略倾斜安装,进料端略高于出料端,筒体可绕轴线转动。运行时废物从较高的一端进入,焚烧残渣从较低一端排出。与余热锅炉共同使用可以回收热分解过程中产生的大量能量,能量额定值非常高。回转窑能有效处理各种不同物态(固体、液体、半固体等)的危险废物,对焚烧废物的适应性强,技术成熟,运行可靠,且运行操作相对简单,可较好满足各种危险废物焚烧在进料、出渣、燃烧完全等方面的要求。焚烧处理的危险废物,有固态、半固态和液态,因此要求焚烧炉炉型对需处理的物料有广泛的适用性和灵活性。根据本工程特点,选择回转窑焚烧炉较为合适。
东风公司十堰基地工业危险废物处理中心占地面积6.38亩,总投资5200万元,由东风(十堰)环保工程有限公司于2014年1月开工建设。据中心负责人介绍,这一危险废物处理中心具备一整套焚烧处置系统、配套余热利用系统、烟气净化系统、储运系统、给排水系统以及污水处理站。中心将采用危废处理焚烧炉工艺流程图,将危险废物投入到1燃室,进行焚烧处理,焚烧完的危险废物,通过旋转窑的自动旋转,进入到炉渣排放系统。焚烧过程中产生的烟气进入到2燃室,将有毒有害的烟气进行处理。预计日处理能力达20吨,主要为东风公司十堰基地各单位及地方企业处理油漆废渣、油污手套、油污纸张等工业危险废物。