宁夏某电厂#2锅炉末过爆管停机不安全事件分析报告
(一)事件发生前工况2018年02月10日网调令#2机组调停,02月25日调停结束#2机组启动,2月25日14时30分#2机组并网。26日19时00分#2机组AGC
(一)事件发生前工况
2018年02月10日网调令#2机组调停,02月25日调停结束#2机组启动,2月25日14时30分#2机组并网。26日19时00分#2机组AGC指令由488MW降至458MW,随后又升至645MW,19时24分#2机组升负荷至625MW时,主蒸汽压力23.75MPa,主汽温度534℃,主蒸汽流量1953T/H,锅炉给水流量1928T/H,炉膛负压稳定,引风机电流550A,机组运行参数正常;19时58分炉膛负压突然升高(由-106Pa升至+75Pa),两台引风机电流增大,由530A升高至590A,运行人员减少总风量,并将负荷由625MW降至610MW,同时发现末过#8管屛大部分壁温测点快速升高,过热器部分壁温超温报警(大于590℃);20时11分#2机组锅炉给水流量1954t/h,主蒸汽流量1852t/h,给水流量异常大于主蒸汽流量100t/h左右,凝结水补水调门异常开大至100%,四管泄漏系统多点报警,泄漏概率为10%,退出声波吹灰器;20时21分就地检查锅炉左侧末过区域声音异常,判断为锅炉左侧末过发生泄漏,立即解除机组AGC控制,快速降负荷至330MW维持运行,向网调申请停机;27日15时45时#2机组打闸停机。
二、检查情况
(一)运行方面
1. 调取#2炉启机过程运行曲线(见图1),爆管前末过11屏未发生超温运行情况。
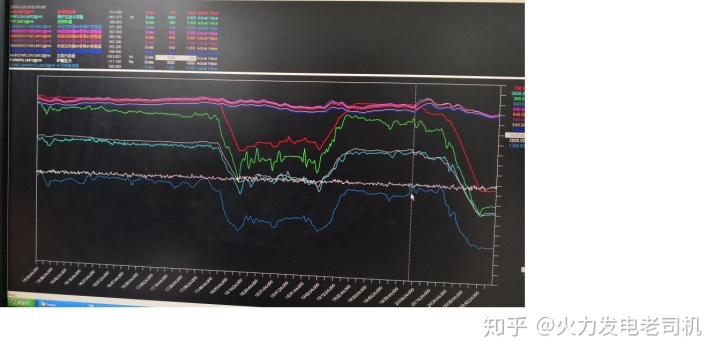
2. 调取启机运行曲线(见图2、3),在机组启动过程中未出现过热器壁温异常情况。
3.机组启动阶段02月25日04时50分启动第一台磨煤机时主蒸汽温度变化率为+16.2℃/min; 02月26日19时06分机组负荷458MW升至625MW时,启动磨煤机时主蒸汽温度变化率最大为+7.58℃/min。
(二)检修方面
1.末过爆管部位宏观及测厚检查
末过第11屏第8根(简称11-8)入口段标高62737mm处爆管,11-8爆管后出列穿过第10屏5、6圈、第9屏4、5圈、第8屏4、5圈,将第7屏6、7圈顶出列。吹漏7-5、7-8、8-5,吹损7-9、8-2、8-3、8-4、8-6、8-7、8-8、9-3、9-4、9-5、9-6、9-7、9-8共计13根。第7至11屏由于受爆管瞬间冲击力作用使7-6、7-7、7-8、8-4、8-5、8-7、10-5、11-6、11-7、11-8、11-9、11-10共计12根变形出列。
t:150%�b tf�e�g体;mso-ascii-font-family:Calibri;mso-hansi-font-family: Calibri;color:black'>升至625MW时,启动磨煤机时主蒸汽温度变化率最大为+7.58℃/min。
末过11-8爆口部位规格为Φ51×10mm,爆口位于SA-213T91和SA-213TP347H异种钢焊口靠SA-213T91侧。爆口呈喇叭状,长径(轴向):110mm,短径(径向):75mm,爆口处管段胀粗明显,爆口唇边锋利,有撕裂纹,爆口处管材内、外壁光滑,未见明显的氧化物和纵向裂纹,爆口形貌具有SA-213T91锅炉炉管短期过热爆管的爆口特征。
US>8-� pn�e�g lang=EN-US>8-7、10-5、11-6、11-7、11-8、11-9、11-10共计12根变形出列。
t:150%�b tf�e�g体;mso-ascii-font-family:Calibri;mso-hansi-font-family: Calibri;color:black'>升至625MW时,启动磨煤机时主蒸汽温度变化率最大为+7.58℃/min。
2.末过氧化皮检测
对末过11-8爆口上、下管段和末过8-5吹漏点上管段氧化皮脱落情况进行内窥镜检查发现:管内壁氧化皮脱落痕迹明显,且脱落量较大,由于爆管脱落的氧化皮已被吹出,弯头部位未见残留氧化皮。从管内可以看到管壁未脱落氧化皮与管内壁结合不致密,存在分层、翘起等现象。
在末过入口联箱处对11-1和11-9管圈割管(见图13、14),内窥镜检查11-8管座入口及其入口附近未见异物,对末过入口联箱内部内窥镜反复检查,整体干净,未见异物。
3除了对爆口上、下管段和吹漏点进行检查外,还对#2锅炉分隔屏过热器、末过、末级再热器不锈钢弯头全部进行了检测。经检测、复测、定性、定量分析:未发现氧化皮堆积量占截面大于1/3的弯头,不会阻碍蒸汽介质的通流而影响热交换,故不需要割管清理。相关检查记录见附表1。
'(三)上次调停检修记录
2018年2月11日#2机组调停,对#2锅炉分隔屏过热器、末过、末级再热器不锈钢弯头全部检测。经检测、复测、定性、定量分析:发现末过氧化皮堆积量占截面大于1/3的弯头共计8根,分隔屏过热器氧化皮堆积量占截面大于1/3的弯头共计27根,其余氧化皮堆积量较小不足1/3,不会阻碍蒸汽介质的通流而影响热交换,故不需要割管清理,相关检查记录见附表2。
ine-he� :5�e�gamily:宋体;mso-ascii-font-family:Calibri;mso-hansi-font-family: Calibri;color:black'>时,启动磨煤机时主蒸汽温度变化率最大为+7.58℃/min。
从表2和表3中可以看出:末过管内脱落氧化皮测厚最小值为110μm,最大值达260μm,平均值为152.9μm;分隔屏过热器管内氧化皮测厚最小值为85μm,最大值达200μm,平均值为135.4μm。
(四)金相检验情况:
对#2炉末过取样两根,一根为爆管爆口处的管段(11排第8圈管),另一根取与爆管相邻处的管段(7排第9圈管),将管样送宁夏机械研究院股份有限公司做金相组织、维氏硬度、迎风面拉伸、氧化皮测厚等性能检验,检验结果两管样的抗拉强度、屈服强度、断后伸长率、维氏硬度全部在SA-213TP347H材质的技术指标的合适范围内(详细检验数据见检验报告),管材不存在质量问题,但从内壁氧化皮厚度检测数据来看,3个试样厚度分别为0.22㎜、0.10㎜、0.12㎜。另对爆口边缘母材进行金相组织分析,金相组织为铁素体+碳化物颗粒+少量粒状贝氏体,组织正常;爆口处壁厚明显变薄,爆口边缘锋利,爆口表面存在氧化皮轴向裂纹,该爆口属于短时超温爆口。(具体见附件3:#2锅炉末级过热器管检验报告)
三、爆管处理情况
1.爆管、吹漏、吹损、弯曲、变形管段换管校正
(1)末过11-8爆管,入口段及前后弯头更换共计20米;
(2)末过11-8爆管后吹漏7-5、7-8、8-5,共计更换24米;
(3)对吹损的7-9、8-2、8-3、8-4、8-6、8-7、8-8、9-3、9-4、9-5、9-6、9-7、9-8共计更换45米。
(4)对9-1吹损部位进行补焊。
(5)对末过7-11屏因爆管脱落管卡进行恢复;
(6)对出列管校正恢复。
(7)对12道SA-213T91和SA-213 TP347H异种钢焊口进行热处理及射线检测。
2.防磨防爆检查及缺陷处理
本次检修中,未发现氧化皮堆积量占截面大于1/3的弯头,不会阻碍蒸汽介质的通流而影响热交换,故不需要割管清理。
四、原因分析
根据宁夏机械研究院股份有限公司检验报告结论,此次末过爆管属于短时超温爆管,原因分析如下:
1.在检修过程中,氧化皮检测、清理不到位。通过翻阅检修记录,符合氧化皮检测标准,检测、清理不到位情况可以排除。
2.在启动过程中,壁温、汽温升降速率过大。通过查阅曲线,壁温升降速率1.75℃/min,符合要求;机组启动阶段02月25日04时50分启动第一台磨煤机时主蒸汽温度变化率为+16.2℃/min; 02月26日19时06分机组负荷458MW升至625MW时,启动磨煤机时主蒸汽温度变化率最大为+7.58℃/min。机组启动过程中,第一台磨煤机启动时,主蒸汽温度变化率超标是由设备的特性决定的;升负荷过程中,主蒸汽变化率+7.58℃/min,虽然超过标准值,但是主蒸汽压力、流量大,不会造成氧化皮瞬间脱落堵塞。
3. 根据宁夏机械研究院股份有限公司检验报告,氧化皮厚度最高达到0.22mm,已到生成、脱落的高峰期。同时末过11—8管屏无温度测点,缺少监视手段,无法确认氧化皮脱落时间。
4. 异物堵塞。通过割管与用内窥镜检查联箱未发现异物。
五、暴露问题
1.从机组投产后,检修、运行人员对防止氧化皮的生成和脱落做了大量的工作,并取得了一定的效果,但对氧化皮产生、脱落的周期研究不足。
2.因对氧化皮产生、脱落的周期研究不足和汽水品质中铁离子含量的变化没有引起足够的重视,启动过程中对氧化皮吹扫没有进行方案上的优化。
3.末过管屏温度测点没有全覆盖。
4. 氧化皮产生、脱落的周期研究不够深入,根据氧化皮检测结果没有对割管标准进行优化。
5.以上问题说明技术监督管理不到位。
六、防范措施
1.建立氧化皮生成量和脱落周期模型,为运行和检修提供依据。
2.启动过程中加强对汽水品质中铁离子含量的分析,优化氧化皮吹扫方案。
3.逐步增加末过温度测点,完善监控手段。
4.在#2机组提效增容改造期间对末过管材进行升级。
5.加强技术监督人员关于氧化皮防治的技术交流与学习,对氧化皮产生、脱落机理进行分析与总结,为机组运行和检修过程中防治氧化皮提供技术指导。